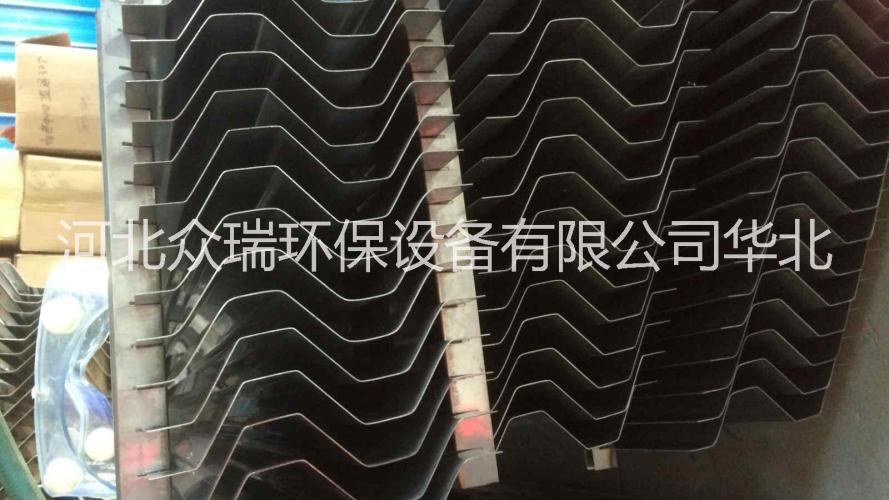
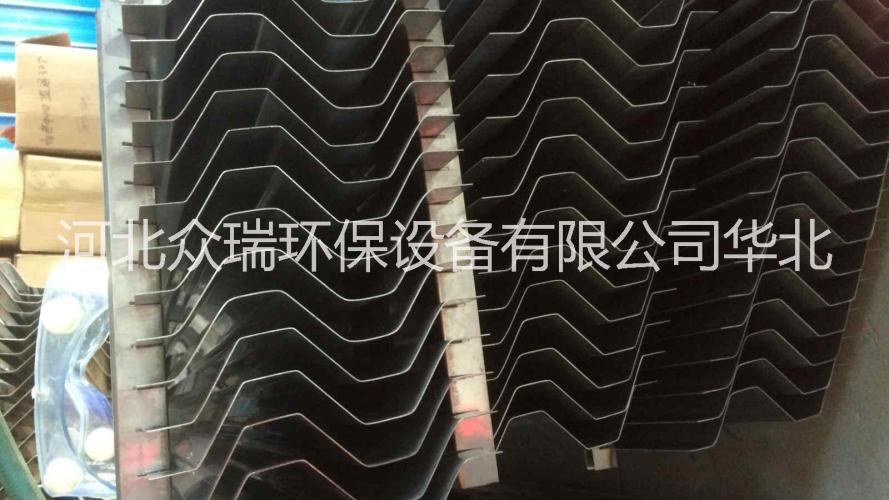
加入世贸后,国际间的竞争日趋激烈,国内经济发展方式逐渐由粗放型向集约型转变,企业由效益型向环保、节能型发展,在此背景下,公司认真落实科学发展观,大力开展节能减排,发展循环经济,策划形成了新上氨肥烟气脱硫项目的重大决策,达到环保、节能的目的。
化工集团进厂原料煤炭含硫量在3%左右,260T/H锅炉出口烟气含硫量一般在4000mg/m3左右,原来主要采用炉内添加石灰石脱硫的方法来降低烟气中的SO2含量,脱硫效果不佳;鉴于环保压力日趋严峻,在对烟气脱硫项目前期充分论证的基础上,与企业实际相结合,新上一套260T/H锅炉烟气脱硫项目作为试点工程,该项目采用氨-肥烟气脱硫技术,技术先进,自动化程度高,易于掌握控制,可操作性强;充分利用了企业内部合成氨系统产生的稀氨水做吸收剂,减少了稀氨水回收过程解析蒸汽,并且回收了内部企业硫酸生产过程副产亚铵溶液,增加了硫铵产量,使集团内部资源优化配置,合理利用。
1. 氨-肥法脱硫技术简介
1.1该技术充分借鉴国内同行业运行中存在的问题,经过充分的考察论证,由××化工设计研究院研发,××化工装备有限公室承建,成功在合成氨自备电站锅炉上实施氨-肥法脱硫的装置,各项运行指标、经济指标在合成氨自备电站锅炉上也处于领先地位。
1.2氨-肥法脱硫技术原理
氨法脱硫技术以水溶液中的SO2和NH3的反应为基础:
SO2+H2O+xNH3 = (NH4)xH2-x SO3 (1)
因此,用氨将废气中的SO2脱除,得到亚硫酸铵中间产品。
将亚硫酸铵氧化为硫酸铵,如反应(2)。
(NH4)xH2-x SO3+1/2O2+(2-x)NH3=(NH4)2SO4 (2)
采用压缩空气对亚硫酸铵直接氧化,并利用烟气的热量浓缩结晶生产硫酸铵,投资低,能耗省。
2. ××化工260T/H烟气脱硫项目简介
××化工260T/H锅炉烟气脱硫工程:烟气脱硫塔部分按1台260吨锅炉配置,脱硫副产物硫酸铵结晶分离包装系统按3台260T/H锅炉配置,该项目采用上述氨-肥法脱硫技术原理,高效吸收塔设备,可大大提高吸收过程的气液比,减少吸收液的循环量,降低循环泵的功耗。
结合厂区260T/H锅炉系统设备具体布置情况,在满足工艺、环保、安全卫生及消防的前提下,尽量布置紧凑,合理利用现有生产设施,充分依托公用工程设施和资源,尽可能使厂房联合、装置集中,节约用地;装置建在260T/H锅炉引风机的右侧空地,由脱硫工段、硫酸铵工段组成,装置区计算占地面积为1000m2;自控设计技术先进、安全可靠、操作方便和经济合理的原则进行,系统操作控制系统采用DCS集中控制,减轻了操作人员的劳动强度。
3. 工艺设计、流程说明和主要技术指标
3.1工艺设计原则和条件
3.1.1严格遵循国家有关法规、规范和现行标准,做到技术先进、经济合理、安全实用、便于管理。
3.1.2结合可持续的科学发展观和企业现状,充分考虑工业需求特点和发展趋势,合理确定工艺参数。作到统筹兼顾、合理安排、切实可行,坚持需要和可能相结合,避免过度投资。
3.1.3坚持科技进步,积极采用新技术、新工艺、新设备,工程设计采用性能好、技术先进、操作方便、可靠耐用的国产工艺设备,降低工程造价,同时确保安全运行。自控仪表以工业计算机集散控制系统动态监控为主,就地检测、指示、记录为辅,适当选用自动化程度较高的仪表。
3.1.4选用成熟的技术,结合××化工具体条件,采用优化设计方法,提高设计水平和降低工程投资额。
3.1.5充分利用现场相应的公用设施、辅助设施,以节约投资,加快工程的建设周期。
3.1.6本技术方案中3台260t/h锅炉脱硫一期工程脱硫装置按一台260T/H锅炉配置,脱硫副产物装置装置按3台260T/H锅炉配置。
3.1.7设计脱硫效率≥98%,脱硝效率不低于20%。
3.1.8吸收液:5-10%稀氨水。
3.2工艺流程说明
锅炉引风机来的的烟气(温度<170℃)进入脱硫塔,高温烟气进入脱硫塔中部的浓缩段,经过除尘、洗涤, 降温至50-60℃,再进入上部吸收段, 气液在其中充分接触,用氨化吸收液循环吸收烟气中的SO2生成亚硫酸铵,脱硫后的烟气(温度50-60℃)由除雾器除去烟气中的水滴,经净烟气烟道回原烟囱排放到大气。
吸收剂氨水与吸收液混合后进入吸收塔,吸收烟气中SO2形成的亚硫酸铵,通过下降管进入吸收塔底部与氧化空气接触反应生成硫酸铵溶液,硫铵溶液通过二级循环泵送入浓缩段,即烟气洗涤降温段,将烟气冷却到55℃,硫铵溶液受热蒸发部分水份得到浓缩,形成固含量(10-20%)的硫铵浆液,去硫铵工序。
固含量10-20%的浆液经结晶泵送至硫铵工序经旋流器浓缩、增稠,脱水后形成固含量40-50%左右的硫铵浆液,清液进入料液槽;固含量40-50%左右的硫铵浆液进入离心机进行固液分离,形成含水2-3%左右的硫铵,母液溢流到料液槽,料液槽内的液体经料液泵送回吸收系统。
3.3主要工艺技术指标
3.3.1脱硫效率≥98%;脱硫后烟气中SO2含量执行《GB13223-2003》,在设计工况下,不高于200mg/Nm3。
3.3.2整套装置运行时间相对于锅炉运行时间的可用率执行《HJ/T179-2005》,脱硫装置可用率不低于98%。装置每年小修一次,每3年大修一次,主体设备设计寿命为30年(不包括易损件:运转设备、阀门、紧固件等)。
3.3.3设计工况下,脱硫的系统总压降(系统进出口压力差)小于1000Pa。
3.3.4脱硫后排放烟气雾滴浓度执行《HJ/T179-2005》不大于50mg/m3。
3.4系统设计消耗定额
序号 |
名称 |
规格 |
单位 |
小时消耗指标 |
年消耗指标 |
1 |
液氨 |
99.6% |
t |
0.527 |
4523 |
2 |
水 |
|
t |
15 |
146030 |
3 |
电 |
380V |
kWh |
445 |
3891270 |
4. 项目建设和投运
4.1建设阶段
260T/H锅炉一期烟气脱硫装置于2007年9月份批复立项,该项目集团自主设计,工业装备公司承建,2007年10月份项目破土动工。项目安装期间,对进厂设备认真组织验收、拆检,对设备、电器仪表等缺陷严格整改,确保设备不出现质量问题;进行图纸会审,确保图纸符合工艺安装要求,严格组织施工,吸取其他厂家运行中存在的问题,对部分工艺进行了调整,在全体项目人员的精诚合作、共同努力下,于5月26日系统并入烟气运行,一次开车成功,宣告工程建设结束。
4.2开车调试、运行阶段
2008年3、4月底开始单机试运并水联动调试消缺,开车调试消缺完成后,5月26日正式向系统投烟气,并加氨水运行,6月4日硫铵系统开车,产出第一袋硫铵。在项目开车调试运行过程中,暴露出不少问题。
如循环泵和结晶泵腐蚀严重、玻璃钢管道漏点多,循环液位不稳定;丝网除雾器阻力大、浓缩段运行中产生积料多;离心机筛网磨损变大出料不正常;浓缩段产生堵塞溢液等,针对出现的问题,多次召开专题会,共同磋商研究,根据生产实际情况对系统进行了调整:
4.2.1对氧化段溢流平衡管进行了改造,有效改进了烟气脱硫运行操作条件。
4.2.2将脱硫塔丝网除雾器更换为折流式除雾器,脱硫进口压力由1.2 KPa降至0.5KPa,除雾器基本无阻力最大100Pa,一段吸收压差0.3KPa,同样负荷下系统压差比原来下降了0.7KPa,新除雾器冲洗水没有带水现象。
4.2.3针对氧化段有时向浓缩段带液的情况,降低了氧化段的溢流管的高度(下降了300mm),开车后没有出现带液现象。
4.2.4浓缩段上溢流口增加冲洗水,倒U形弯管高点增加破虹管,浓缩段底部增加了液位计,方便了运行人员的操作,有效控制了溢液事故。
在项目建设和生产运行管理人员共同努力下,经过不懈的摸索调整,确定了以控制固含量、确保离心机出料为重点,烟气调整为辅助的运行方式;积极推行了新工艺,根据硫铵形成的化学反应机理,根据PH值控制好加氨量,合理控制亚铵加入量和一、二级循环槽亚硫酸铵、亚硫酸氢铵含量,成功地将内部企业副产亚铵加入脱硫液体循环系统,增加了硫铵产量,减少了能源浪费。现今脱硫系统工艺运行稳定,工况烟气量为44.5万立方/小时,烟气中的二氧化硫含量由4000 mg/m3 脱除到 200mg/m3以下,脱硫效率98%以上,硫铵成品达标。
5. 经济效益分析
项目投运后,有效利用了园区尿素系统副产的稀氨水,回收了内部企业副产亚铵溶液,使资源充分利用,年减少SO2排放8403吨,同时可将烟气中的SO2回收,并资源化,生产硫酸铵1.76万吨,实现销售收入1144.6万元;据初步估算,硫铵生产成本在800元/吨左右,硫铵外售价格在950元/吨,年净收益264万元。烟气脱硫投运后,变废为宝,化害为利,具有显著的环境和社会效益。
根据260吨锅炉烟气脱硫的建设及运行经验,集团下属各企业130吨、75吨锅炉都在建设烟气氨法脱硫装置,全部自行设计,自行安装,08年底均可建成投产。