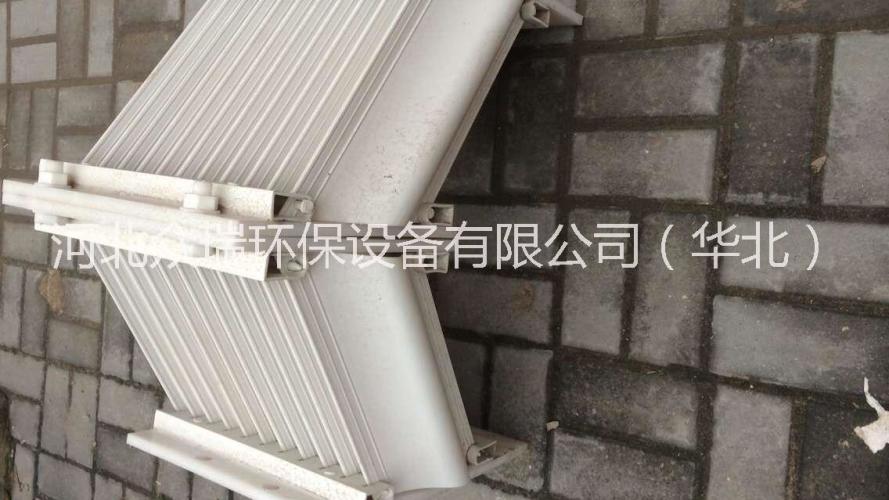
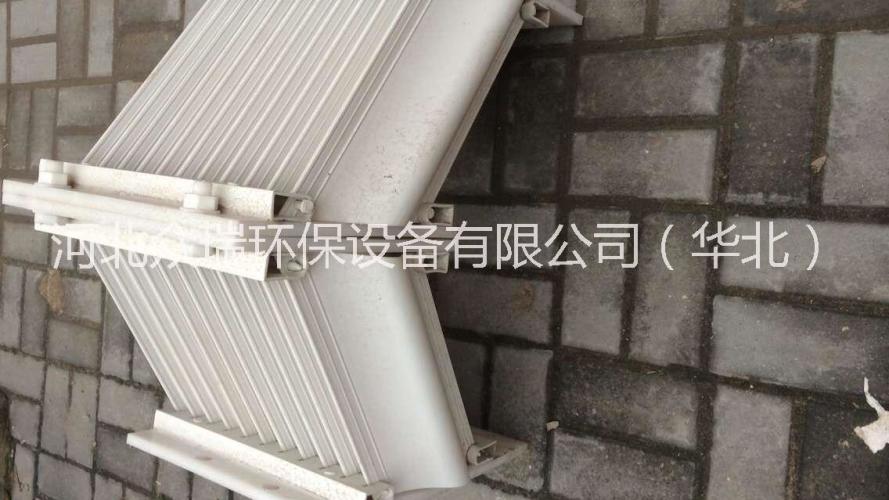
4.1建设阶段
260T/H锅炉一期烟气脱硫装置于2007年9月份批复立项,该项目集团自主设计,工业装备公司承建,2007年10月份项目破土动工。项目安装期间,对进厂设备认真组织验收、拆检,对设备、电器仪表等缺陷严格整改,确保设备不出现质量问题;进行图纸会审,确保图纸符合工艺安装要求,严格组织施工,吸取其他厂家运行中存在的问题,对部分工艺进行了调整,在全体项目人员的精诚合作、共同努力下,于5月26日系统并入烟气运行,一次开车成功,宣告工程建设结束。
4.2开车调试、运行阶段
2008年3、4月底开始单机试运并水联动调试消缺,开车调试消缺完成后,5月26日正式向系统投烟气,并加氨水运行,6月4日硫铵系统开车,产出第一袋硫铵。在项目开车调试运行过程中,暴露出不少问题。
如循环泵和结晶泵腐蚀严重、玻璃钢管道漏点多,循环液位不稳定;丝网除雾器阻力大、浓缩段运行中产生积料多;离心机筛网磨损变大出料不正常;浓缩段产生堵塞溢液等,针对出现的问题,多次召开专题会,共同磋商研究,根据生产实际情况对系统进行了调整:
4.2.1对氧化段溢流平衡管进行了改造,有效改进了烟气脱硫运行操作条件。
4.2.2将脱硫塔丝网除雾器更换为折流式除雾器,脱硫进口压力由1.2 KPa降至0.5KPa,除雾器基本无阻力最大100Pa,一段吸收压差0.3KPa,同样负荷下系统压差比原来下降了0.7KPa,新除雾器冲洗水没有带水现象。
4.2.3针对氧化段有时向浓缩段带液的情况,降低了氧化段的溢流管的高度(下降了300mm),开车后没有出现带液现象。
4.2.4浓缩段上溢流口增加冲洗水,倒U形弯管高点增加破虹管,浓缩段底部增加了液位计,方便了运行人员的操作,有效控制了溢液事故。
在项目建设和生产运行管理人员共同努力下,经过不懈的摸索调整,确定了以控制固含量、确保离心机出料为重点,烟气调整为辅助的运行方式;积极推行了新工艺,根据硫铵形成的化学反应机理,根据PH值控制好加氨量,合理控制亚铵加入量和一、二级循环槽亚硫酸铵、亚硫酸氢铵含量,成功地将内部企业副产亚铵加入脱硫液体循环系统,增加了硫铵产量,减少了能源浪费。现今脱硫系统工艺运行稳定,工况烟气量为44.5万立方/小时,烟气中的二氧化硫含量由4000 mg/m3 脱除到 200mg/m3以下,脱硫效率98%以上,硫铵成品达标。
5. 经济效益分析
项目投运后,有效利用了园区尿素系统副产的稀氨水,回收了内部企业副产亚铵溶液,使资源充分利用,年减少SO2排放8403吨,同时可将烟气中的SO2回收,并资源化,生产硫酸铵1.76万吨,实现销售收入1144.6万元;据初步估算,硫铵生产成本在800元/吨左右,硫铵外售价格在950元/吨,年净收益264万元。烟气脱硫投运后,变废为宝,化害为利,具有显著的环境和社会效益。
根据260吨锅炉烟气脱硫的建设及运行经验,集团下属各企业130吨、75吨锅炉都在建设烟气氨法脱硫装置,全部自行设计,自行安装,08年底均可建成投产。
种脱硫技术介绍
目前烟气脱硫技术种类达几十种,按脱硫过程是否加水和脱硫产物的干湿形态,烟气脱硫分为:湿法、半干法、干法三大类脱硫工艺。湿法脱硫技术较为成熟,效率高,操作简单。传统的石灰石/石灰—石膏法烟气脱硫工艺采用钙基脱硫剂吸收二氧化硫后生成的亚硫酸钙、硫酸钙,由于其溶解度较小,极易在脱硫塔内及管道内形成结垢、堵塞现象。双碱法烟气脱硫技术是为了克服石灰石—石灰法容易结垢的缺点而发展起来的。
溶剂萃取法
选择适当的溶剂通过萃取法可以有效地脱除油品中的硫化物。一般而言,萃取法能有效地把油品中的硫醇萃取出来,再通过蒸馏的方法将萃取溶剂和硫醇进行分离,得到附加值较高的硫醇副产品,溶剂可循环使用。在萃取的过程中,常用的萃伞液是碱液,但有机硫化物在碱液和成品油中的分配系数并不高,为了提高萃取过程中的脱硫效率,可在碱液中添加少量的极性有机溶剂,如MDS、DMF、DMSOD等,这样可以大大提高萃取过程中的脱硫效率。夏道宏等人提出了MDS-H2O-KOH化学萃取法,用这三种萃取剂对FCC汽油进行了萃取率及回收率的实验,结果表明该方法在同一套装置中既能把油品中的硫醇萃取出来,还可以高效回收萃取液中的单一硫醇以及混合硫醇,得到高纯度的硫醇副产品,具有很高的经济效益和社会效益。福建炼油化工公司把萃取和碱洗两种工艺结合起来,采用甲醇-碱洗复合溶剂萃取法显著提高了FCC柴油的储存安定性,萃取溶剂经蒸馏回收甲醇后可循环使用。此种方法投资低,脱硫效率高,具有较高的应用价值。
催化吸附法
催化吸附脱硫技术是使用吸附选择性较好且可再生的固体吸附剂,通过化学吸附的作用来降低油品中的硫含量。它是一种新出现的、能够有效脱除FCC汽油中硫化物的方法。与通常的汽油加氢脱硫相比,其投资成本和操作费用可以降低一半以上,且可以从油品中高效地脱除硫、氮、氧化物等杂质,脱硫率可达90%以上,非常适合国内炼油企业的现状。由于吸附脱硫并不影响汽油的辛烷值和收率,因此这种技术已经引起国内外的高度重视。
Konyukhova等把一些天然沸石(如丝光沸石、钙十字石、斜发沸石等)酸性活化后用于吸附油品中的乙基硫醇和二甲基硫,ZSM-5和NaX沸石则分别用于对硫醚和硫醇的吸附。Tsybulevskiy研究了X或Y型分子筛进行改性后对油品的催化吸附性能。Wismann考察了活性炭对油品的催化吸附性能。而在这些研究中普遍在着脱硫深度不够,吸附剂的硫容量较低,脱硫剂的使用周期短,且再生性能不好,因而大大限制了其工业应用。据报道,菲利浦石油公司开发的吸附脱硫技术于2001年应用于258 kt/a的装置,经处理后的汽油平均硫含量约为30 μg/g,是第一套采用吸附法脱除汽油中硫化物的工业装置,并准备将这一技术应用于柴油脱硫。
国内的催化吸附脱硫技术尚处于研究阶段。徐志达、陈冰等用聚丙烯腈基活性炭纤维(NACF)吸附油品中的硫醇,结果只能把油品中的一部分硫醇脱除。张晓静等以13X分子筛为吸附剂对FCC汽油的全馏分和重馏分(>90℃)进行了研究,初步结果表明对硫含量为1220 μg/g的汽油的全馏分和重馏分进行精制后,与未精制的轻馏分(<90℃)混合可得到硫含量低于500 μg/g的汽油。张金岳等对负载型活性炭催化吸附脱硫进行了深入的研究。
总之,催化吸附脱硫技术在对油品没有影响的条件下能有效的脱除油品中的硫化物,且投资费用和操作费用远远低于其他(加氢精制、溶剂萃取,催化氧化等)脱硫技术。因此,研究催化吸附脱硫技术具有非常重要的意义。
络合法
用金属氯化物的DMF溶液来处理含硫油品时可使有机硫化物与金属氯化物之间的电子对相互作用,生成水溶性的络合物而加以除去。能与有机硫化物生成络合物的金属离子非常多,其中以CdCl2的效果最好。下面列举了不同金属氯化物与有机硫化物的络合反应活性顺序为:Cd2+>Co2+>Ni2+> Mn2+>Cr3+>Cu2+>Zn2+>Li+>Fe3+。由于络合法不能脱除油品中的酸性组分,因此在实际应用中经常采用络合萃取与碱洗精制相结合的办法,其脱硫效果非常显著,且所得油品的安定性好,具有较好的经济效益。
生物脱硫技术
生物脱硫,又称生物催化脱硫(简称BDS),是一种在常温常压下利用需氧、厌氧菌除去石油含硫杂环化合物中结合硫的一种新技术。早在1948年美国就有了生物脱硫的专利,但一直没有成功脱除烃类硫化物的实例,其主要原因是不能有效的控制细菌的作用。此后有几个成功的“微生物脱硫”报道,但却没有多少应用价值,原因在于微生物尽管脱去了油中的硫,但同时也消耗了油中的许多炭而减少了油中的许多放热量。科学工作者一直对其进行了深入的研究,直到1998年美国的Institute of Gas Technology(IGT)的研究人员成功的分离了两种特殊的菌株,这两种菌株可以有选择性的脱除二苯并噻吩中的硫,去除油品中杂环硫分子的工业化模型相继产生,1992年在美国分别申请了两项专利(5002888和5104801)。美国Energy BioSystems Corp (EBC)公司获得了这两种菌株的使用权,在此基础上,该公司不仅成功地生产和再生了生物脱硫催化剂,并在降低催化剂生产成本的同时也延长了催化剂的使用寿命。此外该公司又分离得到了玫鸿球菌的细菌,该细菌能够使C-S键断裂,实现了脱硫过程中不损失油品烃类的目的。现在,EBC公司已成为世界上对生物脱硫技术研究最广泛的公司。此外,日本工业技术研究院生命工程工业技术研究所与石油产业活化中心联合开发出了柴油脱硫的新菌种,此菌种可以同时脱除柴油中的二苯并噻吩和苯并噻吩中的硫,而这两种硫化物中的硫是用其它方法难以脱除的。
BDS过程是以自然界产生的有氧细菌与有机硫化物发生氧化反应,选择性氧化使C-S键断裂,将硫原子氧化成硫酸盐或亚硫酸盐转入水相,而DBT的骨架结构氧化成羟基联苯留在油相,从而达到脱除硫化物的目的。BDS技术从出现至今已发展了几十年,目前为止仍处于开发研究阶段。由于BDS技术有许多优点,它可以与已有的HDS装置有机组合,不仅可以大幅度地降低生产成本,而且由于有机硫产品的附加值较高,BDS比HDS在经济上有更强的竞争力。同时BDS还可以与催化吸附脱硫组合,是实现对燃料油深度脱硫的有效方法。因此BDS技术具有广阔的应用前景,预计在2010年左右将有工业化装置出现。
新型的脱硫技术
氧化脱硫技术
氧化脱硫技术是用氧化剂将噻吩类硫化物氧化成亚砜和砜,再用溶剂抽提的方法将亚砜和砜从油品中脱除,氧化剂经过再生后循环使用。目前的低硫柴油都是通过加氢技术生产的,由于柴油中的二甲基二苯并噻吩结构稳定不易加氢脱硫,为了使油品中的硫含量降到10 μg/g,需要更高的反应压力和更低的空速,这无疑增加了加氢技术的投资费用和生产成本。而氧化脱硫技术不仅可以满足对柴油馏分10 μg/g的要求,还可以再分销网点设置简便可行的脱硫装置,是满足最终销售油品质量的较好途径。
(1) ASR-2氧化脱硫技术
ASR-2氧化脱硫技术是由Unipure公司开发的一种新型脱硫技术,此技术具有投资和操作费用低、操作条件缓和、不需要氢源、能耗低、无污染排放、能生产超低硫柴油、装置建设灵活等优点,为炼油厂和分销网点提供了一个经济、可靠的满足油品硫含量要求的方法。
在实验过程中,此技术能把柴油中的硫含量由7000 μg/g最终降到5 μg/g。此外该技术还可以用来生产超低硫柴油,来作为油品的调和组分,以满足油品加工和销售市场的需要。目前ASR-2技术正在进行中试和工业实验的设计工作。其工艺流程如下:含硫柴油与氧化剂及催化剂的水相在反应器内混合,在接近常压和缓和的温度下将噻吩类含硫化合物氧化成砜;然后将含有待生催化剂和砜的水相与油相分离后送至再生部分,除去砜并再生催化剂;含有砜的油相送至萃取系统,实现砜和油相分离;由水相和油相得到的砜一起送到处理系统,来生产高附加值的化工产品。
尽管ASR-2脱硫技术已进行了多年的研究,但一直没有得到工业应用,主要是由于催化剂的再生循环、氧化物的脱除等一些技术问题还没有解决。ASR-2技术可以使柴油产品的硫含量达到5 μg/g,与加氢处理技术柴油产品的硫含量分别为30 μg/g和15 μg/g时相比,硫含量和总处理费用要少的多。因此,如果一些技术性问题能够很好地解决,那么ASR-2氧化脱硫技术将具有十分广阔的市场前景。
(2) 超声波氧化脱硫技术
超声波氧化脱硫 (SulphCo)技术是由USC和SulphCo公司联合开发的新型脱硫技术。此技术的化学原理与ASR-2技术基本相同,不同之处是SulphCo技术采用了超声波反应器,强化了反应过程,使脱硫效果更加理想。其流程描述为:原料与含有氧化剂和催化剂的水相在反应器内混合,在超声波的作用下,小气泡迅速的产生和破灭,从而使油相与水相剧烈混合,在短时间内超声波还可以使混合物料内的局部温度和压力迅速升高,且在混合物料内产生过氧化氢,参与硫化物的反应;经溶剂萃取脱除砜和硫酸盐,溶剂再生后循环使用,砜和硫酸盐可以生产其他化工产品。
SulphCo在完成实验室工作后,又进行了中试放大实验,取得了令人满意的效果,即不同硫含量的柴油经过氧化脱硫技术后硫含量均能降低到10 μg/g以下。目前Bechtel公司正在着手SulphCo技术的工业试验。
氨法烟气脱硫的特点
1、适用范围广,不受燃煤含硫量、锅炉容量的限制。
由于吸收剂氨比石灰石或石灰活性大,并且在设计时也考虑留有一定的裕度,因而氨法除尘装置对煤质变化、锅炉负荷变化的适应性强。这在我国能源供应紧张、来什么煤烧什么煤的情况下,更显现出它的优势。氨法脱硫的特点之一是煤中含硫越高,硫酸铵的产量就越大;同时,煤也越便宜,业主所得到的利润就越大。
2、脱硫效率很高,很容易达到95%以上。脱硫后的烟气不但二氧化硫浓度很低,而且烟气含尘量也大大减少。
3、吸收剂易采购,可有三种形式:液氨、氨水、碳铵。
4、氨法脱硫装置对机组负荷变化有较强的适应性,能适应快速启动、冷态启动、温态启动、热态启动等方式;适应机组负荷35%BMCR~100%BMCR状态下运行。
5、国内外有成功运行的实例,运行可靠性好,无结垢问题发生。
6、氨是良好的碱性吸收剂,吸收剂利用率很高。
从吸收化学机理上分析,SO2的吸收是酸碱中和反应,吸收剂碱性越强,越有利于吸收。氨的碱性强于钙基(石灰石,石灰)。从吸收物理机理上分析,钙基吸收剂吸收SO2是气-固反应,反应速度较慢,而且反应不完全,吸收剂利用率低;为此需要将其磨细、雾化、循环等过程以提高吸收剂的利用率,但将使整个系统能耗增加。而氨吸收SO2是气-液反应或气-气反应,反应速率快,反应完全,吸收剂利用率高,脱硫效率也高。仅就吸收过程而言,与钙基吸收设备相比,氨吸收设备体积较小,能耗也低。虽然吸收塔内循环液为硫酸铵饱和溶液,但由于硫酸铵极易溶于水,并且有硫酸铵晶种的存在,实践中未出现结垢、堵塞的问题。
7、副产品硫酸氨价值高,经济效益好
氨法烟气脱硫的副产品是硫酸铵,正是中国广大耕地所需要的含氮含硫的肥料。它可以单独使用,也可以和其他营养元素一起做复合肥料,有着广阔的市场需求。不象钙基脱硫副产品石膏或亚硫酸钙,或因其市场饱和,或因其无法使用,抛弃后还占用宝贵的土地资源,形成“石头搬家”现象。一吨氨可以生产四吨96%以上的硫酸铵化肥,按目前我们调研的行情,三吨硫酸铵化肥价值就可抵消一吨氨的费用,还能剩下一吨硫酸铵成为盈余。如果进一步用硫酸铵同氯化钾反应得到硫酸钾和氯化铵,产品附加值还会有显著提高。
8、环境效益好
(1)无废水、废渣和废气排放
工艺过程中为了保持吸收液里的氯离子浓度低于20g/l,以减少溶液对设备部件的腐蚀,需要不断的将含有氯化铵(NH4Cl)溶液排向副产品干燥器里使其蒸发,得到的固体氯化铵也是肥料,但其量是很小的,混在硫酸铵里不会对其质量产生影响。另外,还有很少量的飞灰出现在旋流器的溢流里,为了保证副产品硫酸铵的质量,往往需要不间断的用压滤机清除。这部分量是很小的,而且是烟气中原有的。
(2)避免钙基脱硫为获取吸收剂而开山凿石,用煤将其烧制成石灰;在石灰烧制过程中,放出大量的二氧化碳(CO2),既破坏环境又污染了空气。
(3)氨法烟气脱硫是一种综合利用和资源回收的方法。中国硫资源并不丰富,每年要从国外进口200-300万吨硫磺,耗资十多亿元人民币。但中国每年从烟气排走的硫就约有1000万吨之多,而中国广大耕地却有30%因缺少硫元素而影响着粮食的增产。使用氨法烟气脱硫既是综合利用又回收了硫资源,轻松地解决了上述这个矛盾。
9、适合中国的国情
中国是发展中国家,是人口众多的农业大国。氨的资源丰富,每年氨的产量达3600多万吨,世界第一。有400多个生产氨的化肥厂,产地遍及全国各地,河南心连心化肥有限公司本身就是化肥厂,它主要用于农业做肥料用。中国耕地经调查大面积缺硫(在土壤里硫含量<6×10-10即为缺硫),联合国粮油组织已确定除了氮(N)、磷(P)、钾(K)外,硫(S)是植物第四营养元素,它能显著使农作物和蔬果增产。在欧美硫和氮、磷、钾一样卖钱,它的需求量和磷一样多。
我们用氨法进行燃煤烟气脱硫得到副产品硫酸铵肥料,氨是从肥料中来,又回到肥料中去,不影响氨的平衡使用。中国本身就有广阔的市场,据农业权威部门介绍,中国每年需要硫酸铵化肥约400万吨,目前每年只生产60万吨,需求平衡相差甚远。所以说,氨法烟气脱硫完全适合中国能源、农业的发展和环境综合治理的国情。