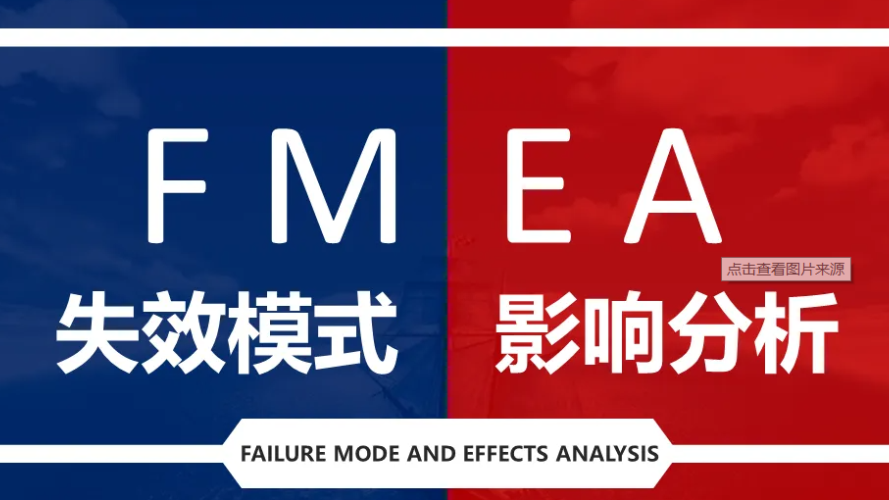
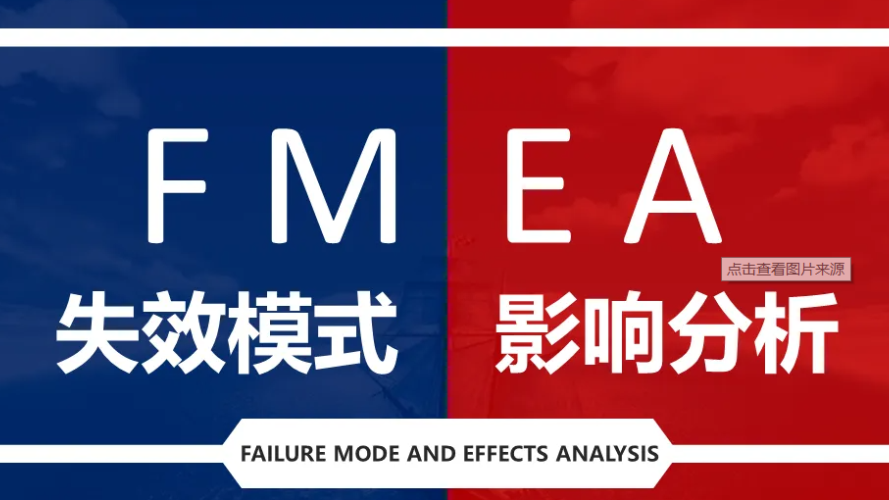
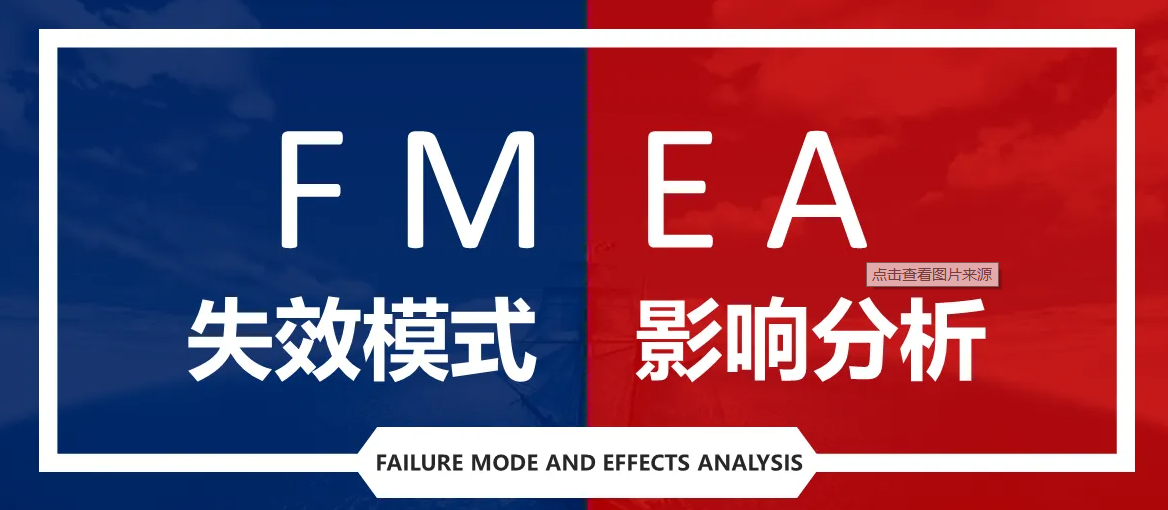
FMEA的发展 FMEA技术的应用发展十分迅速。50年代初,美国一次将FMEA思想用于一种战斗机操作系统的设计分析,到了60年代中期,FMEA技术正式用于航天工业(Apollo计划)。1976年,美国国防部颁布了FMEA的军用标准,限于设计方面。70年代末,FMEA技术开始进入汽车工业和医疗设备工业。80年代初,进入微电子工业。80年代中期,汽车工业开始应用过程FMEA确认其制造过程。到了1988年,美国联邦航空局发布咨询通报要求所有航空系统的设计及分析都必须使用FMEA。1991年,ISO-9000推荐使用FMEA提高产品和过程的设计。1994年,FMEA又成为QS-9000的认证要求。目前,FMEA已在工程实践中形成了一套科学而完整的分析方法。 图片 二 FMEA的基本概念 在设计和制造产品时,通常有三道控制缺陷的防线:避免或消除故障起因、预先确定或检测故障、减少故障的影响和后果。FMEA正是帮助我们从一道防线就将缺陷消灭在摇篮之中的有效工具。 FMEA是一种可靠性设计的重要方法。它实际上是FMA(故障模式分析)和FEA(故障影响分析)的组合。它对各种可能的风险进行评价、分析,以便在现有技术的基础上解决这些风险或将这些风险减小到可接受的水平。及时性是成功实施FMEA的重要因素之一,它是一个“事前的行为”,而不是“事后的行为”。为达到佳效益,FMEA必须在故障模式被纳入产品之前进行。 图片 FMEA实际是一组系列化的活动,其过程包括:找出产品/过程中潜在的故障模式;根据相应的评价体系对找出的潜在故障模式进行风险量化评估;列出故障起因/机理,寻找预防或改进措施。 由于产品故障可能与设计、制造过程、使用、承包商/供应商以及服务有关,因此FMEA又细分为设计FMEA、过程FMEA、使用FMEA和服务FMEA四类。其中设计FMEA和过程FMEA最为常用。 图片 三 设计FMEA 设计FMEA(也记为d-FMEA)应在一个设计概念形成之时或之前开始,并且在产品开发各阶段中,当设计有变化或得到其他信息时及时不断地修改,并在图样加工完成之前结束。其评价与分析的对象是最终的产品以及每个与之相关的系统、子系统和零部件。需要注意的是,d-FMEA在体现设计意图的同时还应保证制造或装配能够实现设计意图。因此,虽然d-FMEA不是靠过程控制来克服设计中的缺陷,但其可以考虑制造/装配过程中技术的/客观的限制,从而为过程控制提供了良好的基础。 进行d-FMEA有助于: ▼设计要求与设计方案的相互权衡; ▼制造与装配要求的最初设计; ▼提高在设计/开发过程中考虑潜在故障模式及其对系统和产品影响的可能性; ▼为制定可靠、有效的设计试验计划和开发项目提供更多的信息; ▼建立一套改进设计和开发试验的优先控制系统; ▼为将来分析研究现场情况、评价设计的更改以及开发设计提供参考。 图片 四 过程FMEA 过程FMEA(也记为p-FMEA)应在生产工装准备之前、在过程可行性分析阶段或之前开始,而且要考虑从单个零件到总成的所有制造过程。其评价与分析的对象是所有新的部件/过程、更改过的部件/过程及应用或环境有变化的原有部件/过程。需要注意的是,虽然p-FMEA不是靠改变产品设计来克服过程缺陷,但它要考虑与计划的装配过程有关的产品设计特性参数,以便最大限度地保证产品满足用户的要求和期望。 p-FMEA一般包括下述内容: ▼确定与产品相关的过程潜在故障模式; ▼评价故障对用户的潜在影响; ▼确定潜在制造或装配过程的故障起因,确定减少故障发生或找出故障条件的过程控制变量; ▼编制潜在故障模式分级表,建立纠正措施的体系; ▼将制造或装配过程文件化。
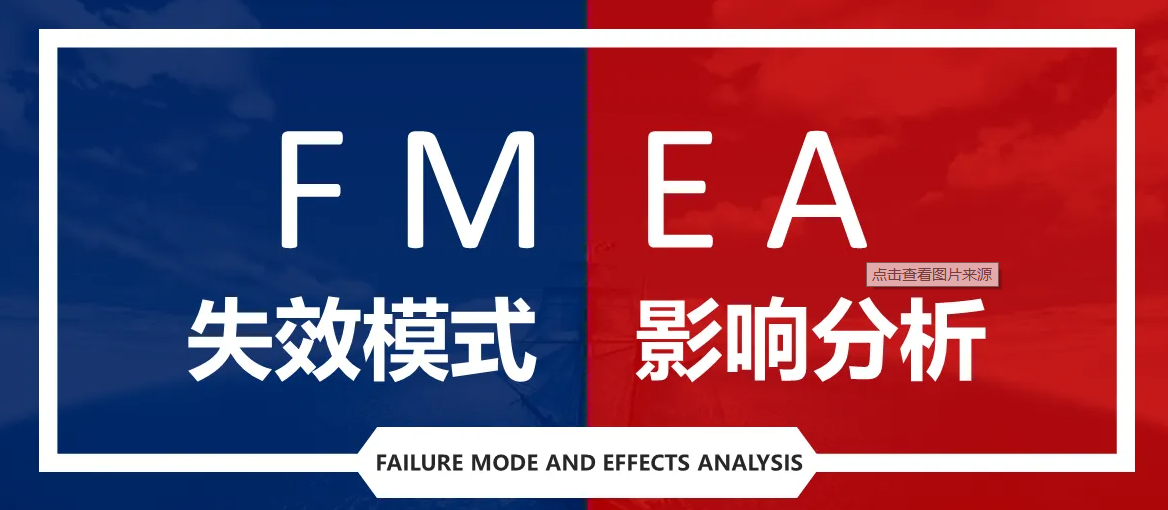
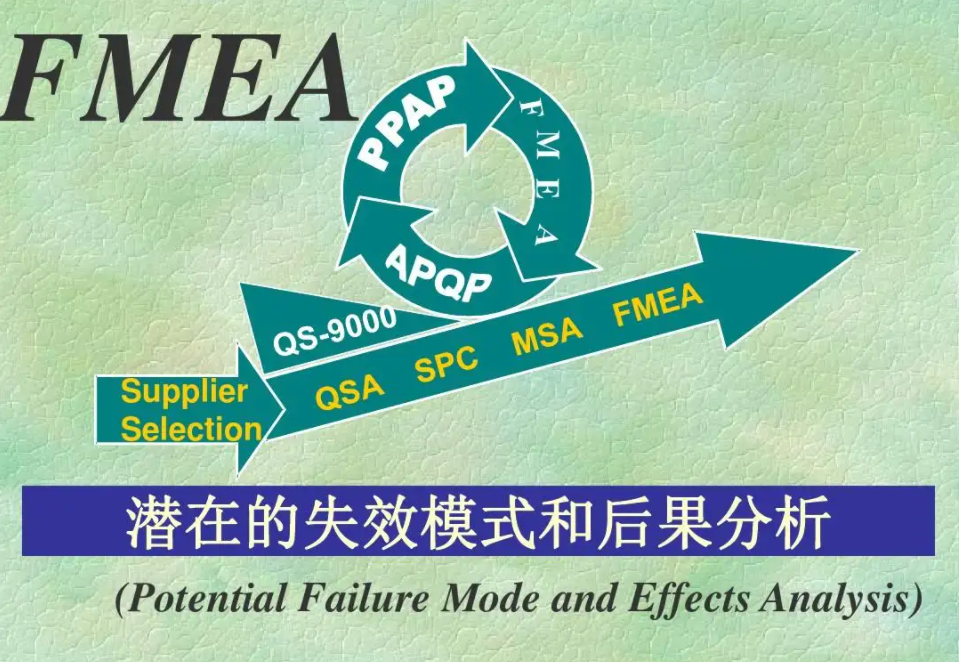
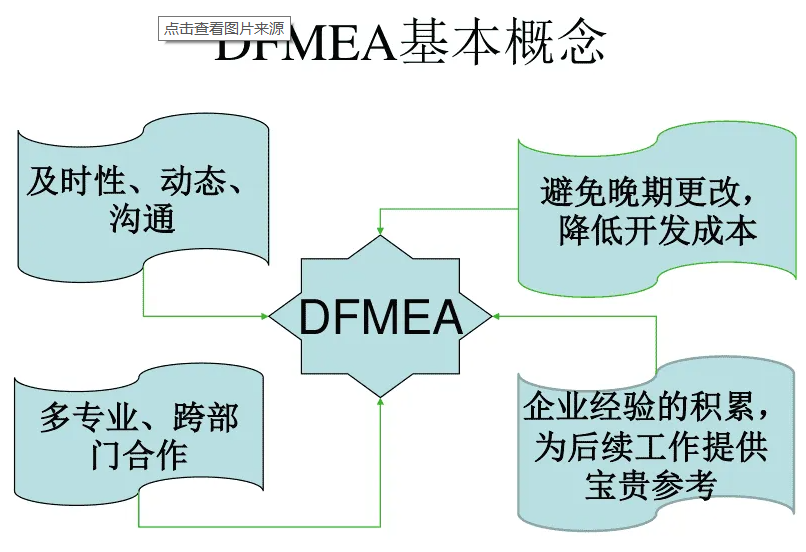
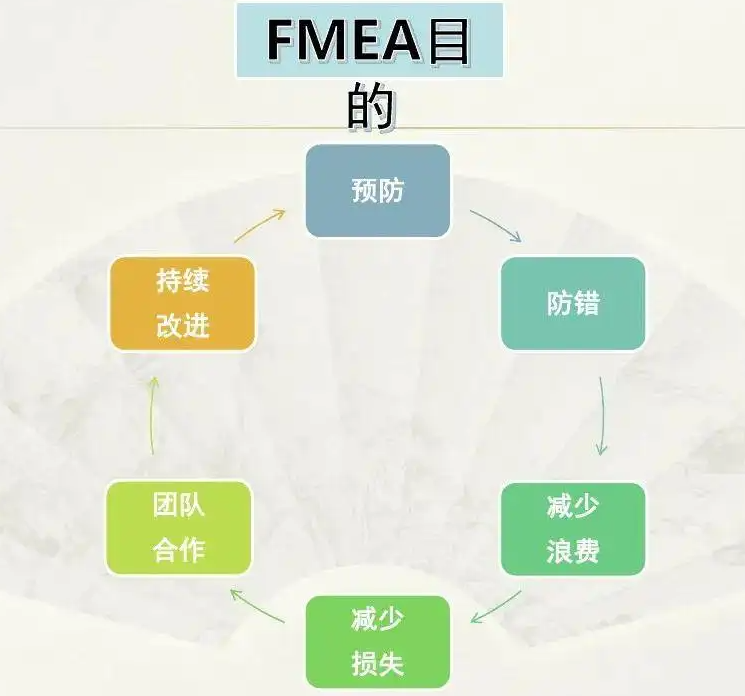